What is Porosity in Welding: Best Practices for Avoiding Permeable Welds
What is Porosity in Welding: Best Practices for Avoiding Permeable Welds
Blog Article
The Science Behind Porosity: A Comprehensive Overview for Welders and Fabricators
Recognizing the intricate systems behind porosity in welding is important for welders and makers making every effort for flawless workmanship. From the structure of the base materials to the intricacies of the welding process itself, a wide range of variables conspire to either intensify or ease the visibility of porosity.
Recognizing Porosity in Welding
FIRST SENTENCE:
Assessment of porosity in welding exposes important insights into the integrity and high quality of the weld joint. Porosity, identified by the presence of dental caries or gaps within the weld steel, is a typical issue in welding processes. These gaps, if not appropriately attended to, can jeopardize the structural integrity and mechanical residential properties of the weld, bring about possible failings in the completed product.
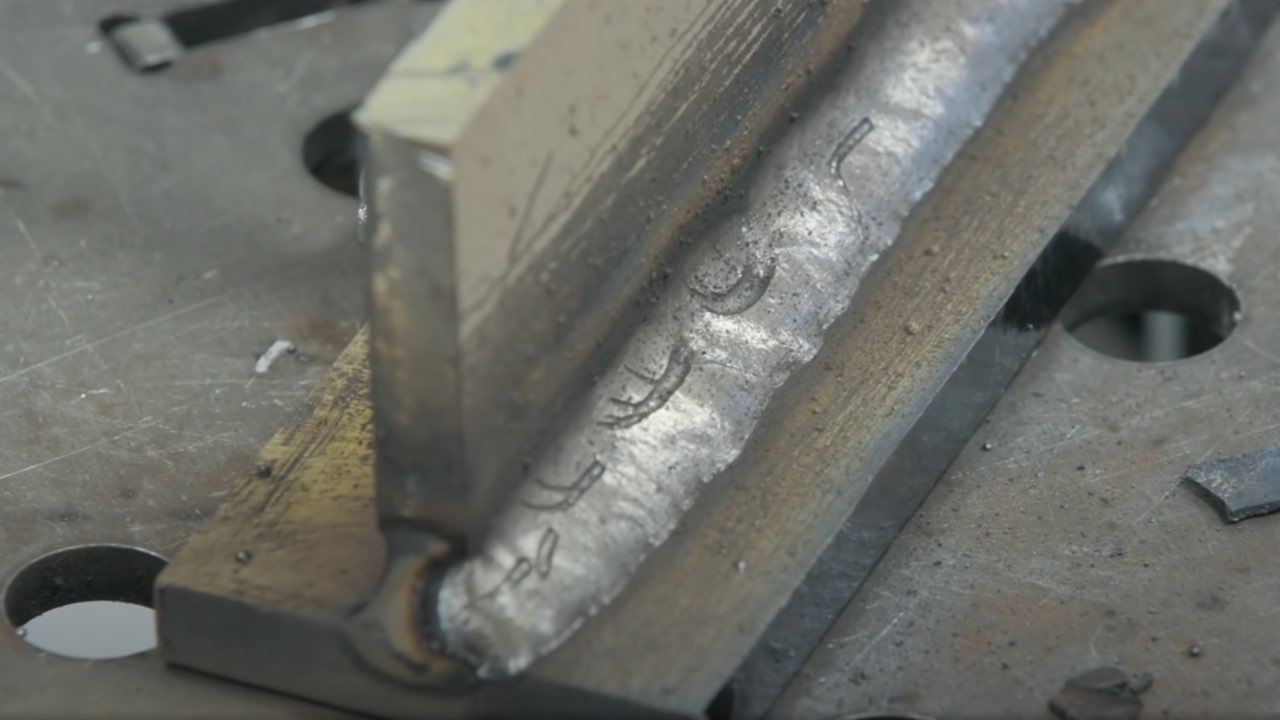
To spot and evaluate porosity, non-destructive screening techniques such as ultrasonic testing or X-ray examination are commonly utilized. These techniques permit for the identification of internal issues without jeopardizing the integrity of the weld. By evaluating the size, form, and distribution of porosity within a weld, welders can make enlightened choices to enhance their welding processes and attain sounder weld joints.

Variables Affecting Porosity Formation
The occurrence of porosity in welding is influenced by a myriad of elements, varying from gas shielding efficiency to the complexities of welding specification setups. Welding parameters, including voltage, present, take a trip speed, and electrode type, likewise effect porosity formation. The welding method used, such as gas metal arc welding (GMAW) or shielded metal arc welding (SMAW), can influence porosity formation due to variations in warm circulation and gas insurance coverage - What is Porosity.
Effects of Porosity on Weld Quality
Porosity development dramatically compromises the structural integrity and mechanical residential properties of bonded joints. When porosity exists in a weld, it creates spaces or tooth cavities within the product, minimizing the total toughness of the joint. These gaps act as tension concentration points, making the weld much more prone to cracking and failure under load. The existence of porosity likewise deteriorates the weld's resistance to rust, as visit homepage the caught air or gases within deep spaces can respond with the surrounding setting, causing destruction with time. In addition, porosity can prevent the weld's capacity to withstand stress or influence, more jeopardizing the overall quality and dependability of the bonded structure. In critical applications such as aerospace, automotive, or architectural building and constructions, where safety and durability are critical, the damaging impacts of porosity on weld high quality can have severe consequences, stressing the importance of reducing porosity through appropriate welding strategies and treatments.
Techniques to Lessen Porosity
In addition, utilizing the ideal welding criteria, such as the correct voltage, present, and travel rate, is critical in preventing porosity. Preserving a constant arc size and angle find more throughout welding additionally aids reduce the likelihood of porosity.

Utilizing the suitable welding technique, such as back-stepping or using a weaving movement, can also help disperse warmth try here evenly and reduce the opportunities of porosity development. By executing these techniques, welders can properly reduce porosity and generate top notch welded joints.

Advanced Solutions for Porosity Control
Applying innovative technologies and innovative approaches plays a critical role in achieving remarkable control over porosity in welding processes. In addition, employing innovative welding strategies such as pulsed MIG welding or modified environment welding can likewise help minimize porosity issues.
An additional sophisticated service includes using sophisticated welding tools. For instance, making use of equipment with integrated features like waveform control and sophisticated source of power can improve weld top quality and reduce porosity threats. Additionally, the execution of automated welding systems with precise control over specifications can dramatically reduce porosity flaws.
Additionally, integrating innovative monitoring and evaluation technologies such as real-time X-ray imaging or automated ultrasonic testing can assist in discovering porosity early in the welding process, permitting immediate rehabilitative activities. Overall, integrating these advanced solutions can significantly boost porosity control and enhance the overall quality of welded components.
Conclusion
In final thought, recognizing the scientific research behind porosity in welding is important for welders and fabricators to produce premium welds. By identifying the aspects influencing porosity formation and executing strategies to decrease it, welders can boost the total weld top quality. Advanced remedies for porosity control can better boost the welding procedure and make certain a strong and reputable weld. It is necessary for welders to constantly inform themselves on porosity and execute ideal practices to achieve optimum outcomes.
Report this page